Injection Molding Actions Resources Fast Radius

Injection Molding Actions Resources Fast Radius During production, molten thermoplastic pellets are injected into a metal mold, cooled, and ejected as a fully formed part ready for industrial end use. ordering injection molded parts from fast radius is simple: upload your design to our cloud manufacturing platform™, work with our engineers to optimize your project, and then begin. Injection molding with fast radius fast radius works closely with our network of suppliers to ensure your final parts will meet the needs of your design. at this stage in the injection molding process, we engage our suppliers to provide the model, drawing, notes, and supporting documentation for your part and to place your order.
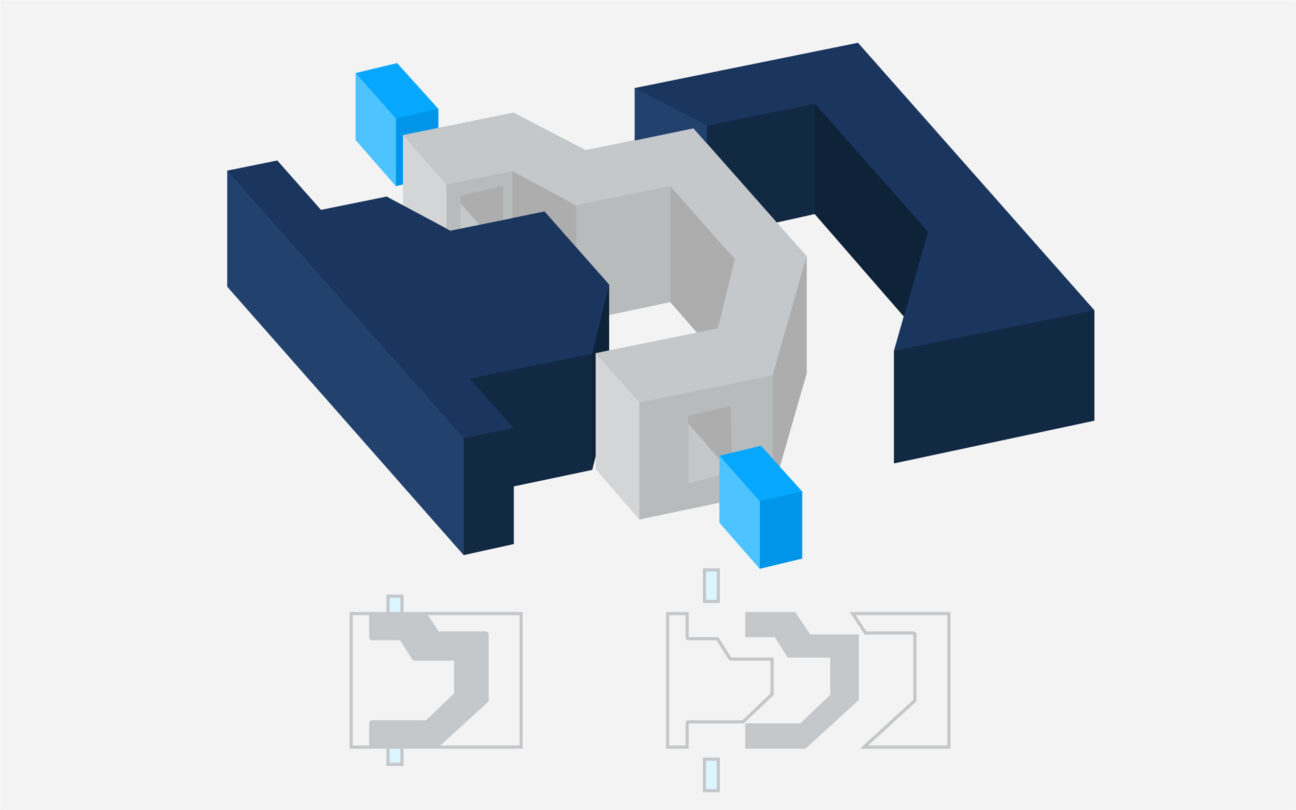
Injection Molding Actions Resources Fast Radius Most common injection molding actions 1. cams cams are simple devices that pull the undercut mold surfaces away from the part, allowing the mold to open. the most common type of cam device uses an angled pin to control the movement of the action, which opens and closes at the same speed as the rest of the mold. cams allow for. Avoid these common injection molding design mistakes. injection molding is a fast, cost effective way to make lots of identical parts, but perfecting your design can be tricky. injection mold adjustments are time consuming and expensive, so you want to get it right the first time. this guide covers: how to avoid undercuts in your part design. The action is inserted into the mold before injection, then unscrewed from the part after the material has set. 5. collapsible core. collapsible core actions are useful for releasing circular undercuts. parts are molded directly around the action, the core of which collapses once the material is set. Applying draft and radii to a part is vital to a properly designed injection molded part. draft helps a part release from a mold with less drag on the part's surface since the material shrinks onto the mold core. limited draft requires an excessive amount of pressure on the ejection system that may damage parts and possibly the mold.
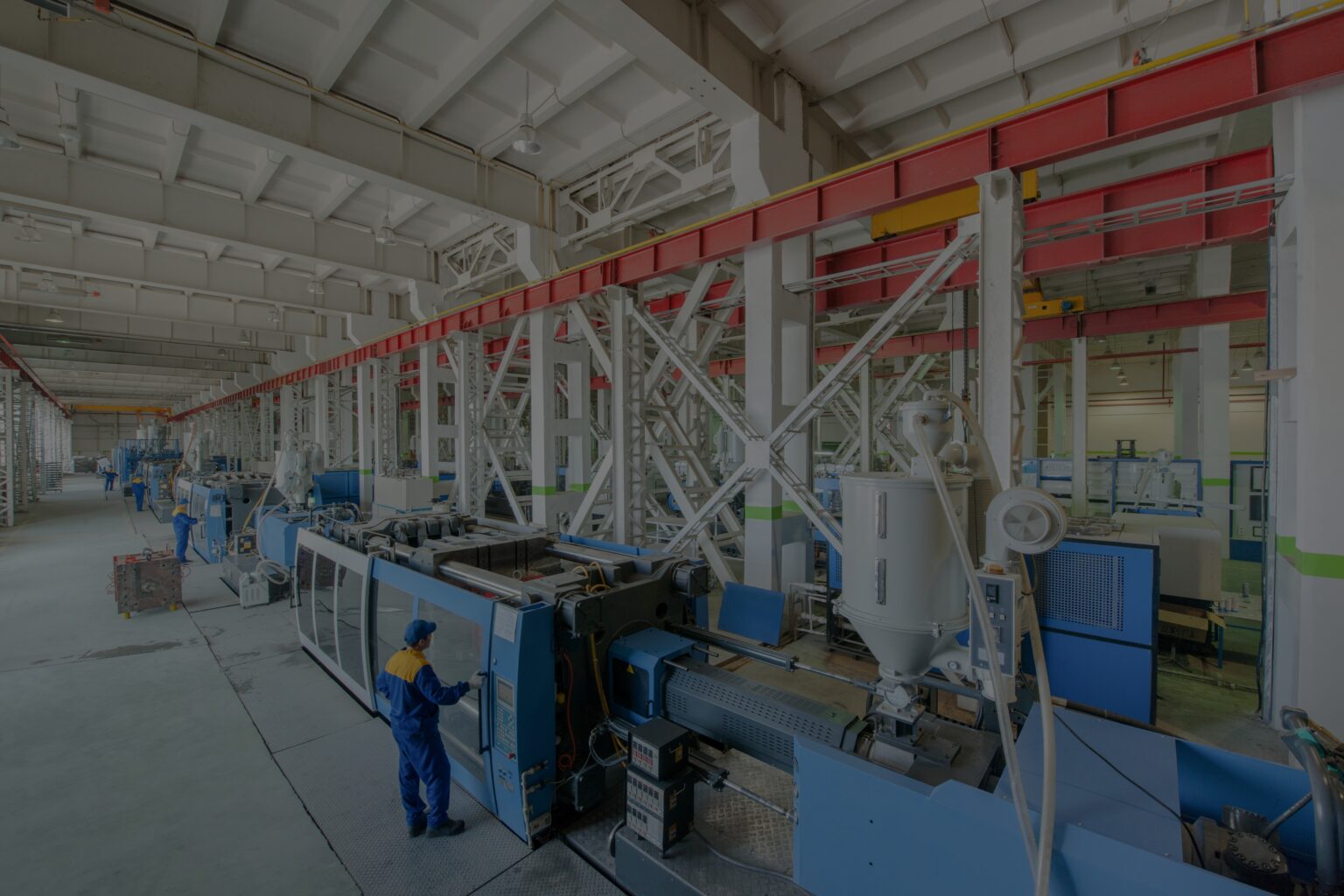
Step By Step Guide To Plastic Injection Molding Fast Radius The action is inserted into the mold before injection, then unscrewed from the part after the material has set. 5. collapsible core. collapsible core actions are useful for releasing circular undercuts. parts are molded directly around the action, the core of which collapses once the material is set. Applying draft and radii to a part is vital to a properly designed injection molded part. draft helps a part release from a mold with less drag on the part's surface since the material shrinks onto the mold core. limited draft requires an excessive amount of pressure on the ejection system that may damage parts and possibly the mold. Rather than leaving these corners sharp, a radius equal to at least 0.5 times the adjacent wall thickness should be used. similarly, the radii at the tops of those walls would be rounded to three times that amount, or 1.5 times the thickness of the nearest wall. this allows molten plastic to flow more easily, and eliminates the residual stress. Assuming that the mold has already been created, injection molding becomes an easily repeatable process consisting of six discrete steps: 1. clamping. the first step of the injection molding process is clamping. injection molds are typically made in two, clamshell style pieces. in the clamping phase, the two metal plates of the mold are pushed.
Comments are closed.