Bonding Thermoplastics Aerospaces Unseen Challenge Keynote From Plastics In Aerospace 2021

юааbondingюаб юааthermoplasticsюаб юааaerospaceюабтащs юааunseenюаб юааchallengeюаб юааkeynoteюаб Fr Michelle woods, thermoplastic specs engineer, interior materials, boeing presents "bonding thermoplastics: aerospace's unseen challenge at plastics in aerosp. Michelle woods received her bachelor of science degree in chemistry from pacific lutheran university in 2007. she joined the boeing team in 2008 and during that time has worked on all aspects of aircraft interiors. in 2018 and 2019, she used a self designed project to mentor university of washington material science engineering students in the.
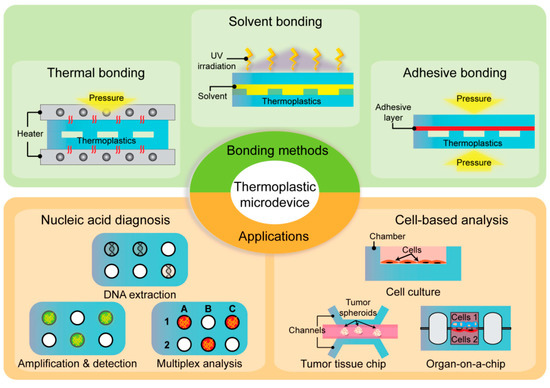
Micromachines Free Full Text Bonding Strategies For Thermoplastics The primary goal of this research program is to develop a framework for the qualification of thermoplastic joints. critical. processing parameters associated with each joining technique will be identified and protocols will be developed for defining. adhesive bonding and welding processes. research tasks include:. Keynote: bonding thermoplastics: aerospace’s unseen challenge michelle woods, thermoplastic specs engineer, interior materials, boeing advanced materials and application development for aircraft interiors provided by sabic’s specialties business ed kung, senior manager, technology & new offerings: specialties lnp compounds. Other in house expertise includes all surface preparation and painting. “we’ve developed very efficient surface prep for thermoplastic composites, which can be difficult to paint and bond,” says leach, noting that atc has also worked on plasma treatment of tpc parts. the company paints 200,000 parts year and edge seals 70,000 parts annually. This chapter covers various polymer composite materials used for aerospace applications. most of the polymer composites in the aircraft are made of thermoset and thermoplastic polymer. reinforcement with engineered fiber in the polymer matrix was found to improve the properties of the polymer matrix. the effects of fiber orientation and the.

Unipace Extends Lsr Bonding To More Thermoplastics Plastics News Other in house expertise includes all surface preparation and painting. “we’ve developed very efficient surface prep for thermoplastic composites, which can be difficult to paint and bond,” says leach, noting that atc has also worked on plasma treatment of tpc parts. the company paints 200,000 parts year and edge seals 70,000 parts annually. This chapter covers various polymer composite materials used for aerospace applications. most of the polymer composites in the aircraft are made of thermoset and thermoplastic polymer. reinforcement with engineered fiber in the polymer matrix was found to improve the properties of the polymer matrix. the effects of fiber orientation and the. At this volume, thermoplastic composites made up about 0.6 percent of total aerostructures (all materials) and about 3.7 percent of total composite shipments. in less than a decade, the aerospace industry has increased its demand for tpcs by roughly 400 percent. this rate of adoption has exceeded previous expectations. Time to heat a carbon composite panel from room temperature up to 400 °c: 3–5 s. maximum welding velocities for common aerospace structures (skin and stringer for example): 2–5 mm s. maximum working power: 3.3 kwh. maximum single lap shear strength: 30–50 mpa depending on thermoplastic matrix.

Pptx Super Plastic Forming And Diffusion Bonding In Aerospace At this volume, thermoplastic composites made up about 0.6 percent of total aerostructures (all materials) and about 3.7 percent of total composite shipments. in less than a decade, the aerospace industry has increased its demand for tpcs by roughly 400 percent. this rate of adoption has exceeded previous expectations. Time to heat a carbon composite panel from room temperature up to 400 °c: 3–5 s. maximum welding velocities for common aerospace structures (skin and stringer for example): 2–5 mm s. maximum working power: 3.3 kwh. maximum single lap shear strength: 30–50 mpa depending on thermoplastic matrix.
Improved Methods For Bonding Aerospace Thermoplastic Composites
Comments are closed.